传统的可靠性设计方法是以经验为主,通过制定可靠性设计准则,并在产品样机设计生产出来之后,进行功能测试和可靠性增长的一些试验,发现了故障或者薄弱环节后,再回到设计环节,修改设计方案,之后再次生产出实物产品后进行验证,如下图所示。
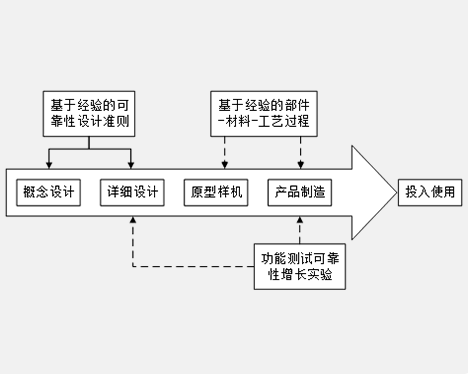
图 传统可靠性设计方法
基于故障物理的可靠性设计过程如下图所示。与传统的可靠性设计方法相比,基于故障物理的方法更注重于量化设计过程。首先要根据产品的情况,总结故障物理设计准则,在产品的概念设计、详细设计阶段,指导定量设计过程。其次在设计阶段,利用故障物理仿真的方法查找设计的薄弱环节,同时进行寿命和可靠性定量计算,并在此阶段,也就是产品制造出来之前,就改进设计,使得产品满足定量设计要求。在设计阶段,产品在投入使用后可能的环境和工作条件是重要的输入信息。最后,在原型实物样机和产品制造环节中,利用定量的部件-材料-工艺设计过程,实现设计的高可靠性。
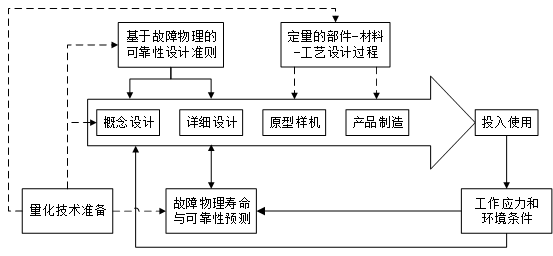
图 基于故障物理的可靠性设计方法
在可靠性设计过程中,需要在性能、材料、封装、机械和电气完整性、成本之间找到最佳的均衡点,因此设计过程是一个迭代的过程。基于故障物理的方法将次迭代过程提前到详细设计阶段(数字样机),而不是在产品制造出来之后再进行,能够大大的节约时间和成本。
对于工程师来说,掌握故障物理方法,在可靠性设计中会有很大的帮助,故障物理是对材料的特性,加工方法,设计中采用的技术的综合描述,同时在产品的整个寿命周期内,这些因素如何与风险因素相互作用,也是故障物理方法的研究范畴。可靠性设计工程师必须要了解产品的使用条件,以及产品与环境之间的相互作用。
定量设计的一个重要依据就是故障机理的各影响因素与寿命和可靠性之间的关系,也就是利用故障物理模型进行计算和分析。例如,要对大规模集成电路进行可靠性设计,就要了解包括电迁移、热载流子、闩锁、ESD等故障机理的定量物理模型,了解设计相关的物理参数与故障之间的关系,这已经成为集成电路设计工程师们总结的一个重要经验。